Making a Basic 5S Worksheet for Thrift
What regularly gets measured gets better
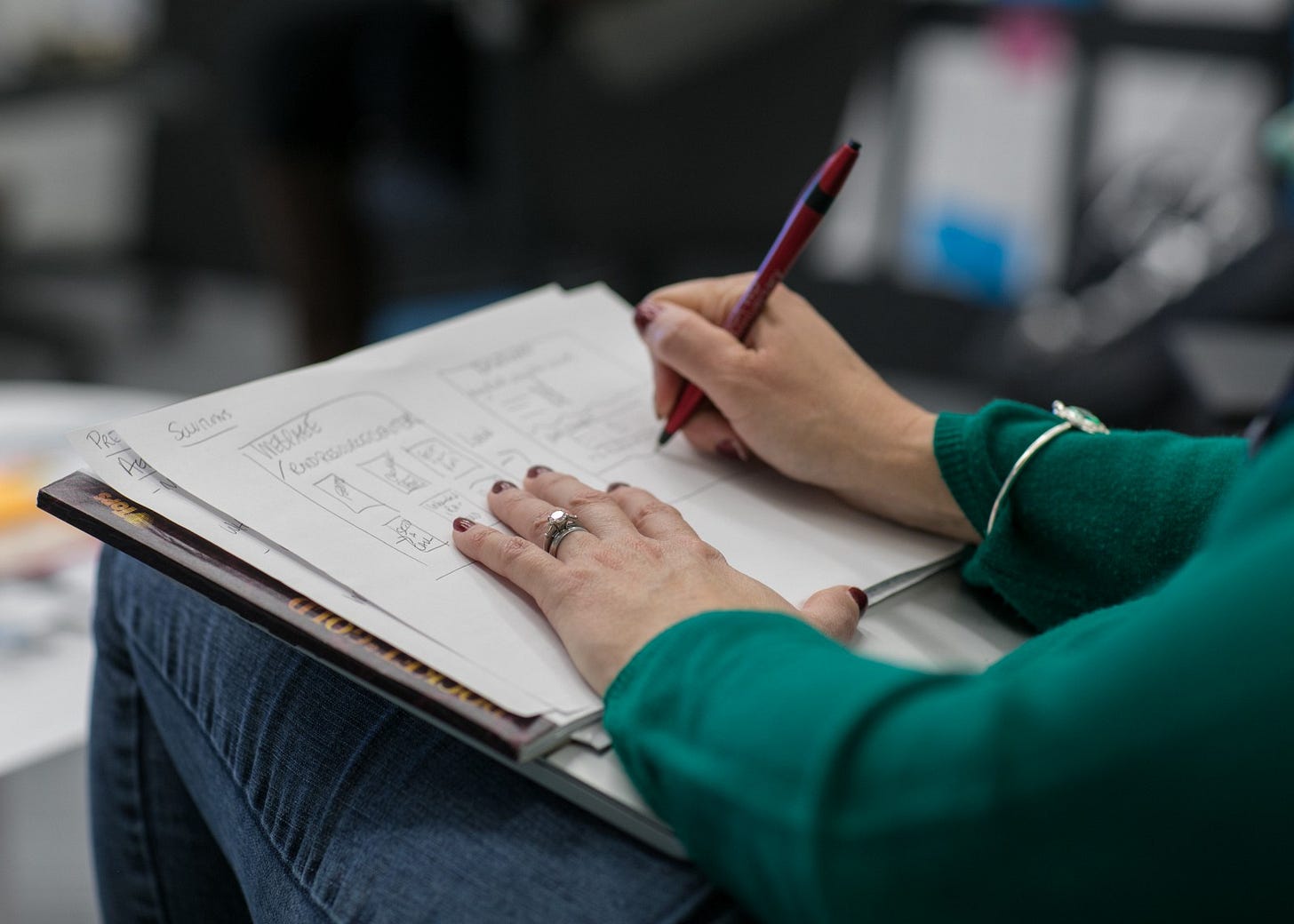
5S Checklists are simply a way to ensure consistency at various workstations. It doesn’t matter if it’s a one-person station or it’s used by multiple people on multiple shifts.
“If you have seen one thrift store, you have seen one thrift store.” The same is true of sorting and processing systems and stations.
A workstation can be anything from the checkout area, to donation acceptance, to processing, to offices, to testing, even the truck. These work best when they are customized for each workstation. Still, there are common themes.
The basics:
What station is this for?
Are all work tools present and working?
Are the proper numbers of tools available? (Not too many or few)
Are adequate supplies stocked? (Not too many or few)
Are foreign goods removed to their proper departments?
Is the area swept and clean?
Is the station 100% ready for the next shift?
Completed by
Verified by
Breaking it down:
Are all work tools present and working?
Every tool and piece of equipment should be fixed as soon as an issue is discovered and be working at the end of every shift.
Are the proper numbers of tools available? (Not too many or few)
From pens to printers, what is needed for a shift should be present. I don’t know what it is about pens, but it seems like there are either 100 or none. Three or so are all that should be needed in a day.
Are adequate supplies stocked? (Not too many or few)
Sounds simple. Thrift seems to attract more than our fair share of hoarders, which includes supplies. Keep everything needed for a shift or two and no more. Excess supplies should be stored in a general supply area away from the workstation.
Are foreign goods removed to their proper departments?
Foreign goods are any merchandise that isn’t worked in that space. For example, when sorting textiles everything from purses to belts, to glassware can show up. It all needs to be taken to the proper work area. Cash register areas are particularly susceptible to this issue.
Is the area swept and clean?
It’s easy to think cleaning is the core of 5S, it isn’t. It’s one thing that pulls other things together. Clean means work surfaces, shelving, floor, equiptment, and even that the trash can is empty.
Is the station 100% ready for the next shift?
This pulls it together. As noted, it doesn’t matter if only one person or multiple people work during multiple shifts. Starting a day at a clean ready to go station sets a positive tone. 100% means 100%.
Completed by
This is simply accountability.
Verified by
More accountability.
Leveling up:
Have the checklist filled out every day, every shift. Regularly check reality against the checklist.
A supplement to the checklist is a standard setup sheet. It includes a list of what should be in the workstation, how much, and where they go.
Make it a habit, a daily expectation.
One suggestion:
If you are new to this idea, set this up in one or two areas, teach the concept, refine it before applying it across the entire store. My suggestion, the checkout area (it’ll make for a more pleasant checkout experience) and the cash office. Clutter and accounting never play well together.
Lots of ways to connect with me:
I am happy to connect on LinkedIn.
Check out some great custom artwork at my Redbubble site.
You can also find me on Pinterest.
I also write on a variety of topics on Medium.