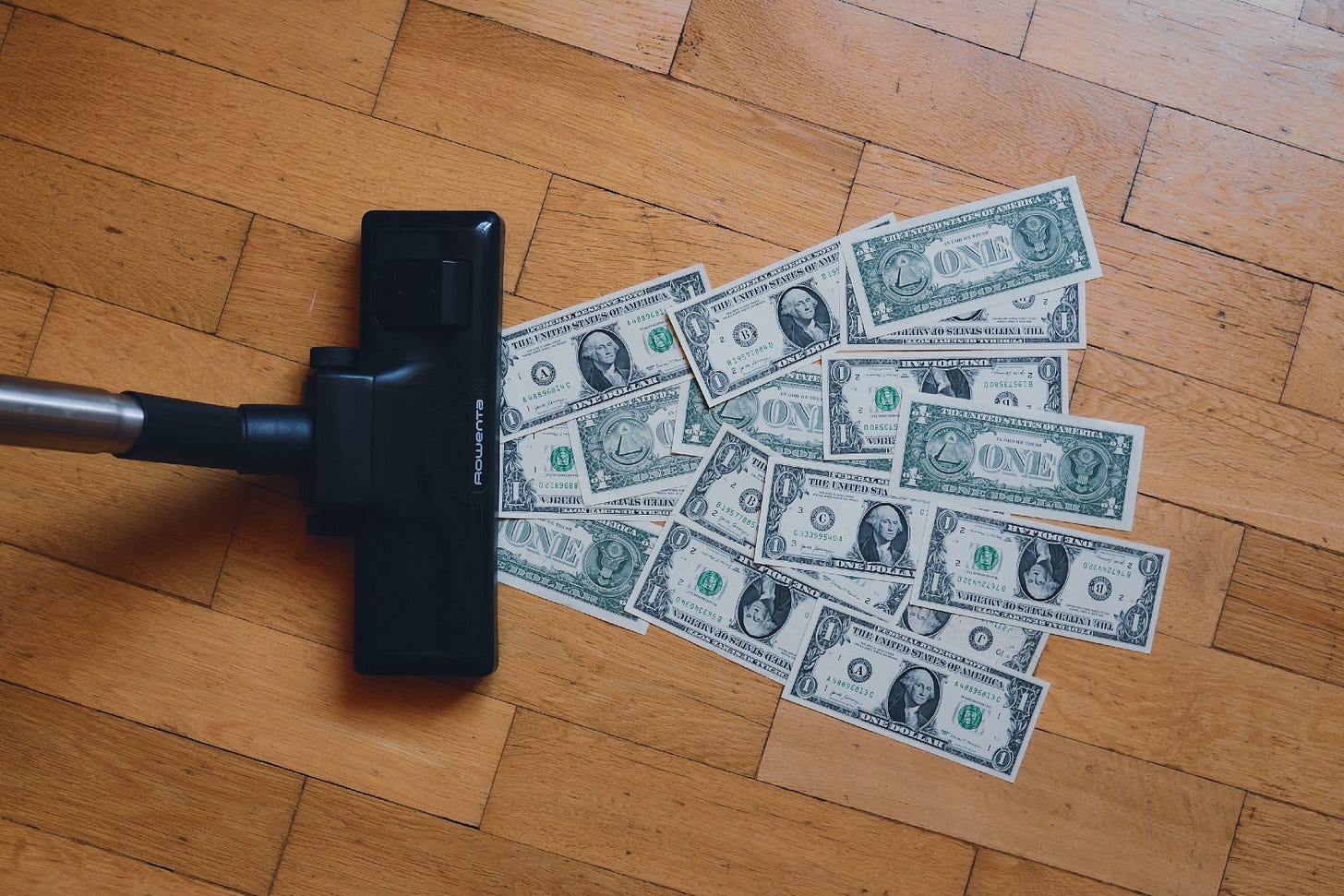
Besides pricing, a sales floor full of fresh goods is key to making money in thrift. Well, retail in general. Even a garage sale does better when it has a lot of stuff.
Want to increase your customer visits, keep goods coming to the sales floor.
24/7 big box stores are much the same. If there are empty pegs and holes all over the shelving people eventually go elsewhere. Early in my career, I had a boss that loved to say “we don’t sell pegboard”. Sure enough, he was right.
“Miss a day, miss a deal” should be a real thing.
What is the difference between production and productivity?
Hint: Production is how much gets done and productivity is how efficiently it gets done.
Always knowing how much of what goes to the sales floor is mission-critical information. Lots of things become visible when production and productivity are tracked consistently.
My greatest retail success has revolved around simply keeping the sales floor full and fresh. No matter the format.
Easier said than done, still has to be done.
Traditional retail knows what’s going on with their stuff. Computer tracking of the inventory level of every item, item velocity, near real-time sales, and on and on. There are a few POS systems trying to match that level of detail in thrift. Short of spending a bucket of money on one of those POS systems what to do?
One way or another that production has to be measured against the labor cost of getting it there.
Production is a function of productivity. What was the labor cost to get X amount of merchandise on the sales floor? Ten people taking 8 hours each to put a total of 1,000 items on the floor may not be good. Ten people putting a total of 10,000 pieces on the floor might be amazing. Unless that information is specifically tracked, who knows? More importantly, knowing how much each person contributed helps manage.
Let’s break down those extremes:
10 people, 80 labor hours. Let’s say $15 per hour, which gets you to a $1,200 cost for the day. Divide that by the number of pieces processed and you at $1.20 labor cost per item for that thousand items. If your average item sells for $5, your production labor cost is 24%. Not counting the rest of the staff and all those other pesky expenses. If you sell through is 50% as it is in many thrift stores that actual cost doubles. Yikes!
If that same staff produces that 10,000 items in a day, guess what, production labor cost is 12¢ per piece. At 50% sell-through, you are still at a quarter.
1,000 items produced per person is 125 per hour. If you don’t think that’s realistic let's dial it back to 75 per hour. That’s 6,000 pieces in a day with a direct labor cost of 20¢ each, or 40¢ at 50% sell-through. 8% production labor cost.
Knowledge truly is power. It’s also profit.
If. you aren’t tracking productivity in a standardized way there are lots of tools out there that you can use.
The links below will take you to some simple spreadsheets I have come up with that might help.
Production Tracking Cheat Sheet
Thanks for reading!
I am happy to connect on LinkedIn.
Check out some great custom artwork at my Redbubble site.
You can also find me on Pinterest.
Check out my Online Sellers book on Amazon.
Tim Gebauer — Thrift Retailer
These are not affiliate links, they are links to items I have created.