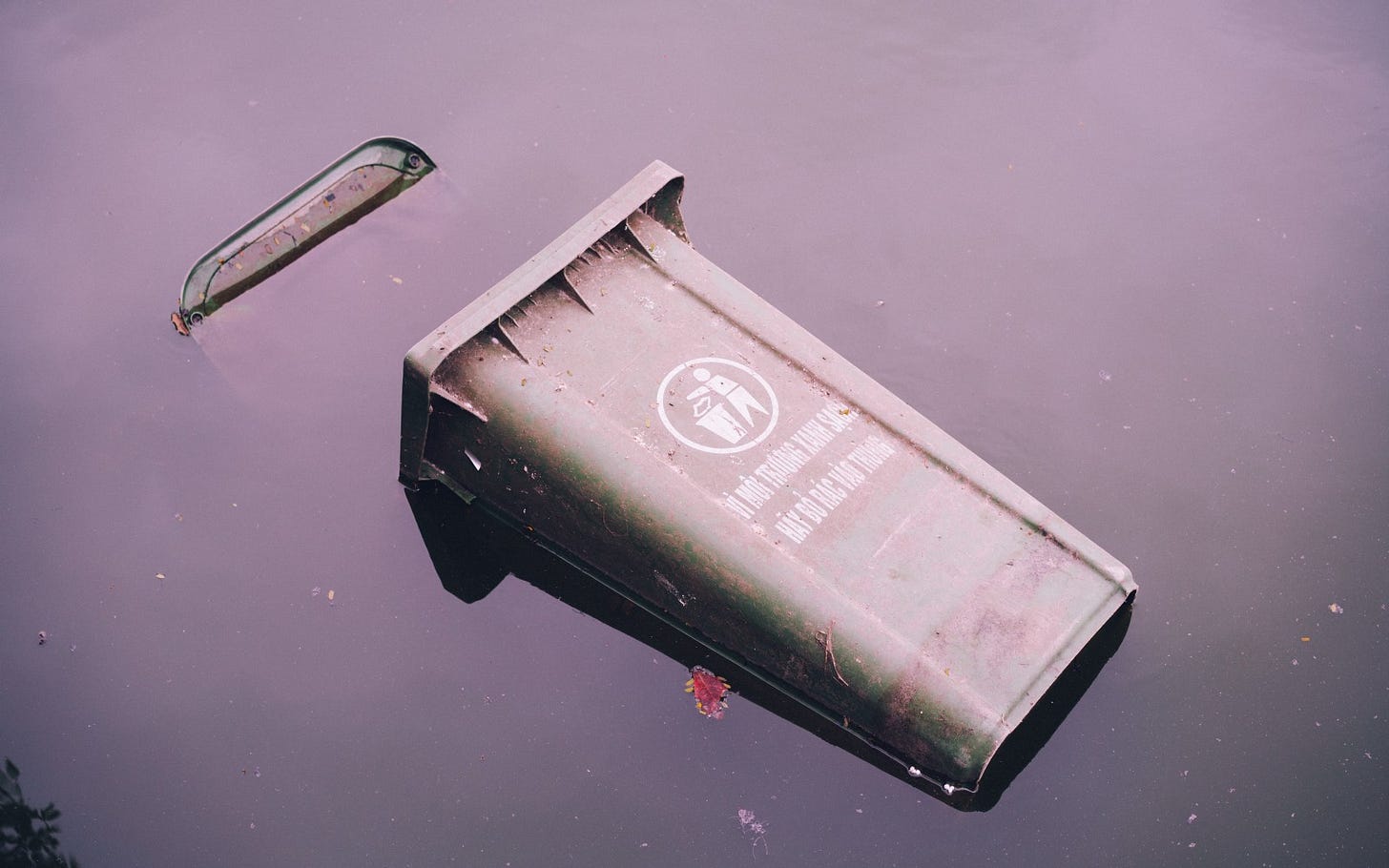
What is that? Great Question. Glad you asked!
It’s a powerful management tool.
A waste walk focuses on one or two of the eight Kaizen causes of waste, yes, while walking around. It’s a purpose-focused version of management by walking around. The key is being informal and spontaneous while looking at specific things.
Years ago I was fortunate enough to occasionally travel with Wal-Mart executives on store visits. I quickly noticed they focused on pretty much the same areas or even items on all of their visits in a week. Those visits might include three stores a day. The areas seemed almost random, but they were intense about their focus points. A Kaizen waste walk works much the same way.
For a first Kaizen waste walk, I suggest a couple of things, Transportation and Motion. They are closely related and are easy to spot if you slow down and take time to see.
Transportation is moving things from point to point. Motion is physical people motion. Equipment placement and availability connect the two.
The higher up in your organization you are the more important it is to leave your possie behind for a waste walk. It’ll be fine, really. You don’t need any filters or spinners with you. You want to see reality and hear from those doing the work.
Watch how people and things move around.
How often do they retrace their steps?
Are all the tools they need to do their job handy?
Is there enough equipment and supplies for everyone?
How far do people have to go to get inventory, equipment, and supplies?
What slows people down?
What sucks up their time unnecessarily?
When talking to staff doing the work ask questions seeking to understand. No judgment, no blame, no snark, just sincere questions. No matter what don’t defend anything. More listening will, over time, generate more unfiltered information. Don’t forget to ask: How would they do whatever?
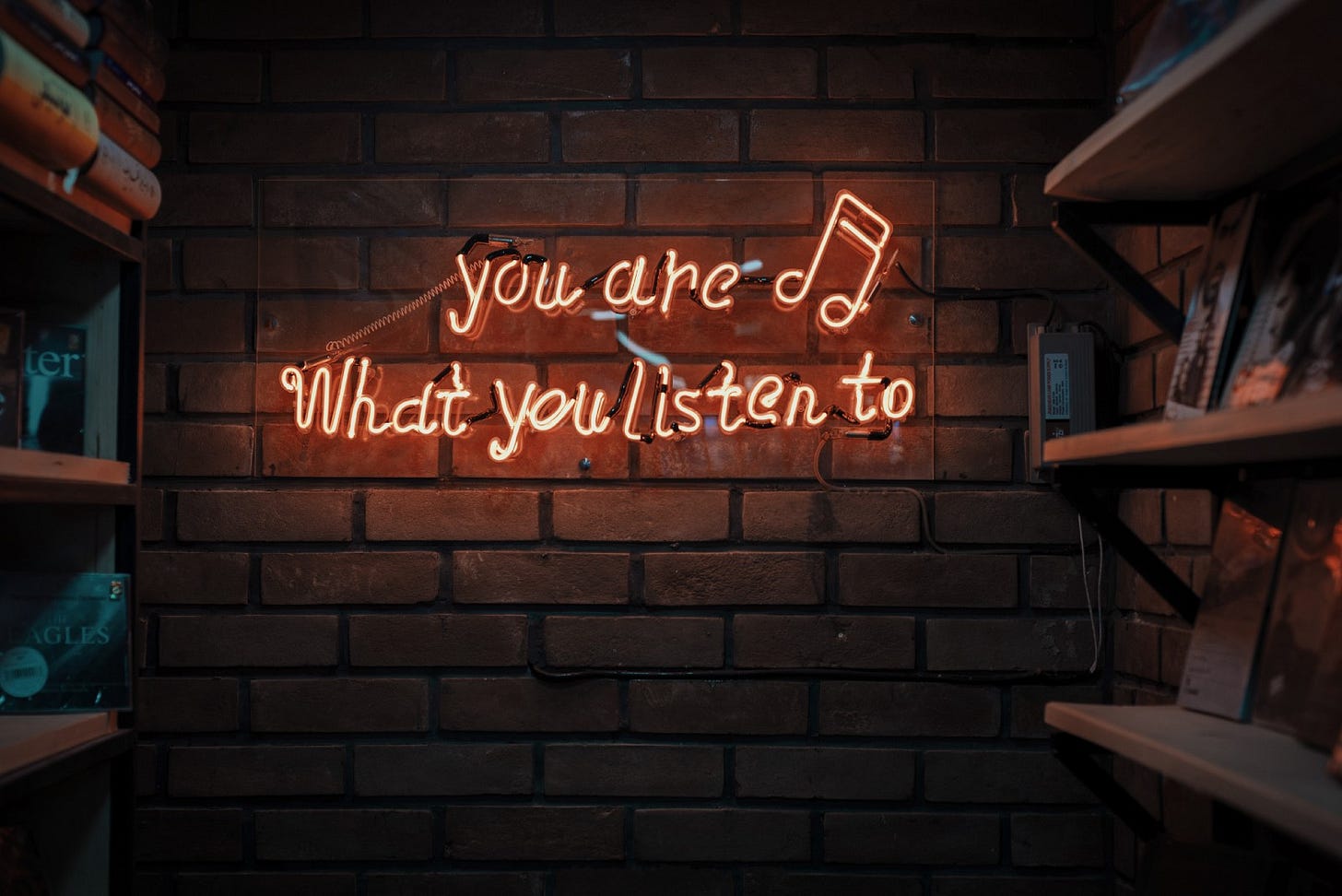
If you have ever seen the TV show Undercover Boss, you will understand how eye-opening honest feedback from line staff can be.
One store I was responsible for only had one pallet jack. One. They needed two regularly and three occasionally. The labor cost of making people wait for their turn (that’s literally what they called it) exceeded the few hundred dollars one of them cost by a factor of ten. So I got them three more. You would have thought it was Christmas.
Most people want to do their jobs, they need the tools to do so.
Work was done faster and friction between departments and staff went down. All for about a thousand dollar investment.
That facility manager was amazing at controlling expenses, in this case, he was being penny wise and pound foolish. That’s something I have seen time and time again, a lack of focus on making sure employees have all the resources they need. Not necessarily all the tools they want, always all they need.
Another location had a supply czar, at least that was my private name for her. You would have thought price stickers were $20 each. People had to regularly stop work, find her, ask for something, prove they really needed it, wait for her to get the minimum she thought they needed, then appreciate her for her generosity. It was crazy.
We took the locked door off of the supply cage. I was sure if we didn’t take the door off the lock would have gone back on. For a while staff hoarded supplies so we eventually had to dial that back with a Kaizen event.
In the end, staff felt more trusted, adequate supplies for a shift or two were always available. More work got done with the same staff. The supply czar suddenly had time to do her actual job.
I have noticed that expense control ninjas tend to prioritize cutting expenses on the front end at the cost of productivity and smooth operations. The irony is that operations with well-supplied organized production staff run better and make more money.
What makes jobs easier and faster?
A little bonus:
When staff starts talking and asks for something, get it for them. In my world, for some reason, working pallet jacks are an often requested item.
When they ask for the why behind something, talk it through with, yes with, them. Seek to understand as a team. You may find there isn’t a good why and something needs to be changed. If so, change it or empower them to do so.
The eight causes of waste in Kaizen/Lean are: Defects, Overprocessing, Waiting, Non Used Talent, Transportation, Inventory, Motion, Excessive production. Also known as D.O.W.N.T.I.M.E.
Lots of ways to connect with me:
I am happy to connect on LinkedIn.
Check out some great custom artwork at my Redbubble site.
You can also find me on Pinterest.
I also write on a variety of topics on Medium.
Check out my Online Sellers book on Amazon.