
Thanks for joining the Thrift Retailer blog, where we talk all things thrift. Welcome to today's episode about basic 5 S concepts in thrift.
5S is a system to keep workplaces organized, standardized, and safe. Since so much random stuff shows up in thrift and second hand it’s even more important to have standard methods in place.
Be careful, start using 5S and you may be sucked into a whole universe of operational excellence. 5S is a key building block in the Kaizen, Lean, and 6sigma universe. The most successful, pleasant, and, yes, profitable thrift operations I have seen are this kind of disciplined.
Everything is either in its place or not. There is a defined process for everything. It's a minimalist lifestyle.
There you have it.
5 S, depending on what you read, are Sort, Set, Shine, Standardise, and Sustain. Safety is often included as the 6th S.
Do them all or don’t do any. Skipping one is like leaving a line of code out of a program, the whole thing breaks down.
Number 1. Sort.
Use, store or discard. This applies to the tools, supplies, and equipment used in a workspace as well as the product that goes through it.
In Kaizen 5S, sort is about getting rid of tools, supplies, and equipment that are unnecessary and making sure everything that is necessary is easily accessible in the workspace. Only what is regularly needed to do the job should be in a station or workspace.
For whatever reason, stuff tends to accumulate. No one needs 20 pens, six markers, five pencils, six scissors, a box full of rags, a month’s worth of price tags, and tagger tails at one workstation. I’ve seen it, you probably have as well.
Textile stations, for example, go through a lot of tagger tails. There should always be a good supply but a month’s worth is just clutter. Multiple stations overstocked with a consumable like that adds up to wasted investment. Chances are whoever orders these supplies just checks the storage area, constantly reordering supplies already on site in abundance.
Some questions to ask.
Do you need it and what do you need it for?
How often do you need it?
How much is needed in a day or shift?
An understanding and agreement of what is and isn’t needed in a workspace is the foundation of everything to come. Everything not necessary to complete work has to be removed from and kept out of the workspace.
The staff working in an area must have the most valuable voices. Yet they have to be able to easily explain the value and frequency of any tool or quantity of items needed in the workspace.
In my experience holding Kaizen events, employees working in an area will sometimes argue passionately for odds and ends that they might only need a couple of times a year.
One quirk in second hand is the interesting or curious items that become décor on a workspace. The Star Wars action figure, the clever snarky poster, the vintage whatnot. There are a few problems with allowing these odds and ends to sit.
It creates clutter. An interesting trinket does not add value to the work area and can be a distraction.
If it’s that interesting, it has value and needs to be sold. As soon as an item is donated it becomes the property of and an asset of the store. No different than traditional purchased goods in a traditional store.
The longer something sits the more likely it will be damaged or stolen, costing the store the entire value of the item.
One thing becomes five, then ten. Other workstations do the same and a snowball effect takes charge.
Management offices are no different. One filled with donated curiosities is a terrible example.
Holding on to donated items like this dishonors the intent of the donor.
A best Kaizen or 5S bests practice is to insure that every item touched every day is processed down one of several designated streams. Convert assets to cash, and dispose of the liabilities properly.
Number 2, Set.
Once the clutter and excess are cleared out and there is agreement on what is actually needed, and how much is needed, everything has to have a home. A specific place each thing stays.
Things used often or constantly should be on the top surface easily accessible and in the same place at each station. Lesser used but needed items, like consumables supplies should be under or adjacent to the workspace.
A tagging gun has a specific home. Same for tags, pens, staplers, and anything else needed in the workspace. A maximum and minimum quantity also have to be established and understood.
At the end of this step only needed items to remain. Each has a designated, marked spot and a maximum quantity is established.
Once all that is worked out it is time to focus on the donated stuff. The goal is to create a constantly flowing stream with a minimum number of rocks in that stream.
One caveat is often between right and left-handed people. Some accommodation may be appropriate in those cases.
Everything goes in one of these directions:
Sell
Store
Test
Research
Salvage
Trash
Just as every tool and supply has to be defined, the flow of goods through various stages also has to be defined. A river is a great visualization. Rivers don’t loop over themselves. Those that meander back and forth are great for tubing but not so much for the efficient flow of goods from donation to sale.
A couple of ways to measure efficiency is to map the number of times an item is touched, how long an item is touched, and importantly, how long an item waits between steps. Goods spend most of their time waiting between steps.
Number 3, Shine.
Everything is clean — Eventually, this becomes a point of pride.
Getting things clean is one thing. Keeping things clean is the key. This makes a workplace pleasant and reinforces the other pillars of 5S.
Clean includes the floor, work tables, tools, carts, and everything related to a work area. It’s also important to regularly inspect tools and equipment, making sure they are in good shape, and ready to go.
Scheduling time in the work day just for shine, and clean signals how important it is and gives permission to leave a work area clean and ready for the next shift or day. It is so much easier to come to work knowing a work area is organized, clean, and set up.
Management regularly reinforces, and from time to time participating in this step will help turn it into a habit.
One pet peeve of mine is price stickers. They have a way of accumulating. When they are cleaned up every shift they don’t multiply overnight.
Number 4. Standardize (create rules)
This is how agreed-to layouts and processes are maintained. There are several ways to accomplish this.
Use visuals to maintain norms. This can include marking where each item is maintained in a workstation.
Signing or pictures showing the proper layout of a workstation can also be useful.
Marking exactly where work in process is kept and how much is allowed keeps an area from being overwhelmed.
Use checklists that cover the key points of each of the 5 S expectations. These can be filled out and signed daily by those working in space. They should be verified by management at regular intervals, and done by them from time to time.
Number 5. Sustain.
This is the secret sauce. 5S isn’t a way to clean up a facility, though that may be an initial result. Sustaining involves buy-in at every level. Regular review and updates with a documentation process that is regularly reviewed will make or break this kind of program.
Like any initiative, there will be early adopters that get it. Then there will be those that hate to change no matter the benefits. Celebrate the early adopters and bring the rest along.
Number 6. Safety.
Safety is often the sixth S. It’s a natural result of a successful program.
When everything has a place, and everyone understands and follows clearly defined processes, a facility will naturally be a safer workplace.
The mop and broom are always in the right place, ready for use upon need. Eye wash stations are accessible and current. Aisles are clear of clutter and pallet jacks are stored when not in use.
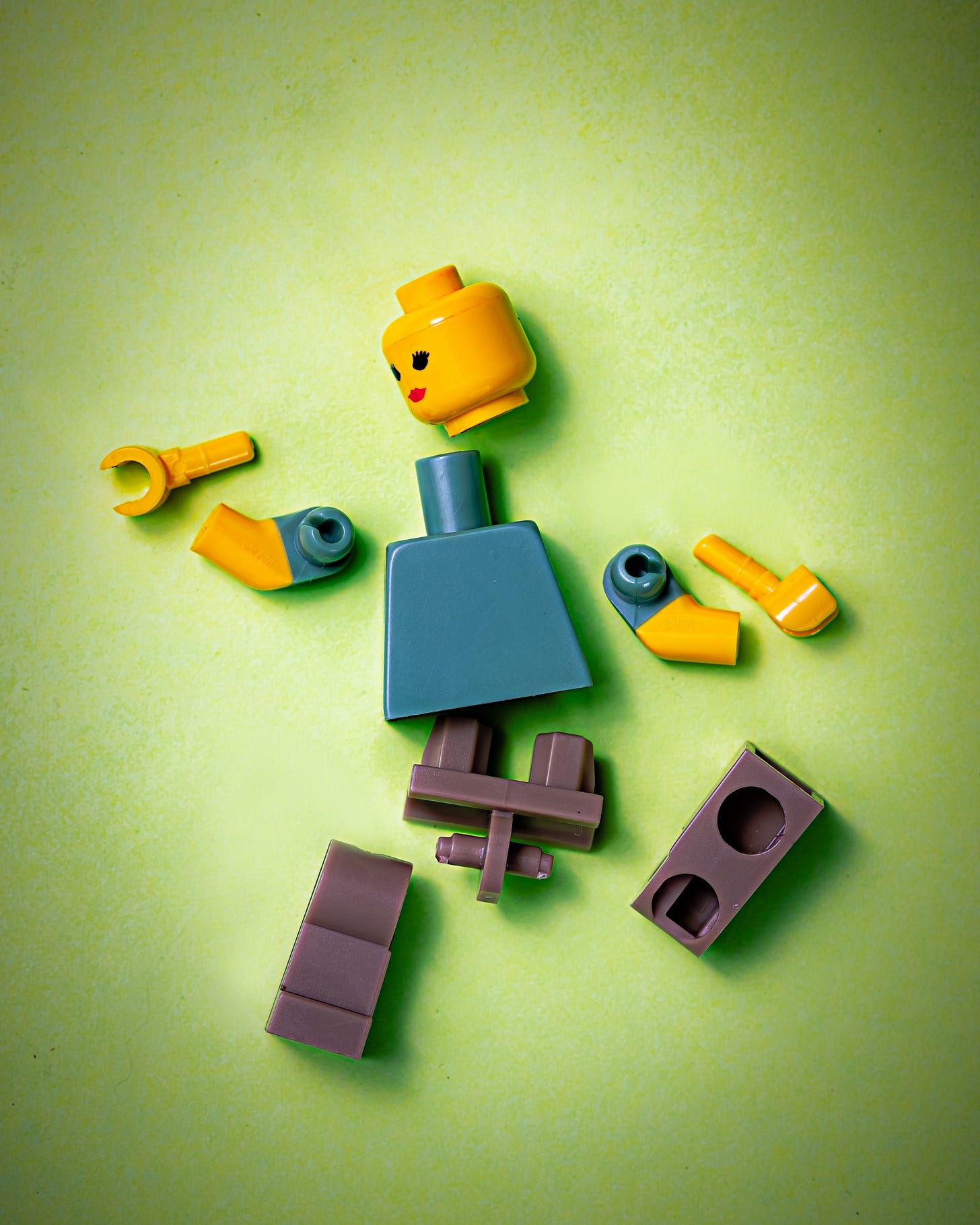
Wow. That was a lot.
Don’t try to change the whole company at once. Pick one area or process, and focus on that. Pull a team together, include a dash of patience and a pinch of determination.